
The objective is to evaluate the fatigue cracking performance of sustainable asphalt materials and mix designs to establish realistic boundaries for high content RAP and reclaimed asphalt shingle (RAS) mixtures employing WMA technologies based on percent binder replacement and binder grade changes. It contains 10 different test lanes with varying amounts of recycled material content.

The current full-scale experiment was built by FHWA in 2013. Two remain to be completed during spring 2017. Eight sites have been successfully tested. Status: Eleven sites were constructed with ten different mixtures. The relative ranking in fatigue cracking as well as supporting laboratory characterization will guide and generate recommendations. Objective: The key project objective is to quantify the cracking resistance of high recycled asphalt pavement (RAP) mixtures that considers the use of lower temperature production with warm-mix asphalt (WMA) and recommend any limitations for combining the two technologies.Īpproach: Construct and load 10 test pavements with different quantities of RAP, different WMA technologies, and different production temperatures at the Pavement Testing Facility. Recent Accomplishments and Contributions Current Full-Scale Projects SUSTAINABILITY: Reclaimed Asphalt PavementĪdvance Use of Recycled Asphalt in Flexible Pavement Infrastructure: Develop and Deploy Framework for Proper Use and Evaluation of Recycled Asphalt in Asphalt Mixtures Services are directed to research and investigations at Turner-Fairbank Highway Research Center (TFHRC) or in cooperation with other government laboratories, agencies, research institutions or associations, with the objective of advancing the knowledge of pavement engineering and the performance of highway materials and structures. All cells are enclosed this allows the water table to be controlled with additional flexibility in testing unbound materials for pavement structures and other geotechnical applications. The test pit contains a reaction frame for load plate testing. Each full-scale test lane is 50 by 4 meters (165 by 13 feet), and can be further divided into 4 subsites, for a total of 48 test locations on the facility grounds.Ī supplemental three cell test pit is available for material testing. The PTF Lab’s main capability is full-scale testing of pavement structures. Two machines allow simultaneous testing of two pavement lanes under the same ambient temperature and moisture conditions or at the same pavement age.

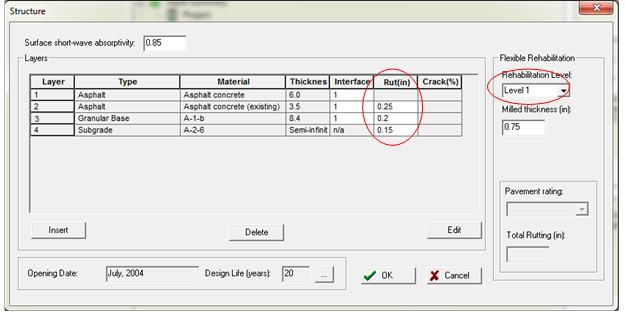

In only a few months, the facility’s loading machines can apply wheel loads comparable to many years of service, and collect the corresponding pavement distress and performance data. The facility simulates truck traffic with controlled loading and pavement temperatures. Past and potential future applications include assessing the impact of different tire or load configurations on pavement performance.
#FHWA PAVEMENT DESIGN SOFTWARE VERIFICATION#
Recent testing has contributed to the development and verification of new specifications, designs, and test procedures for rigid and flexible pavements. The Pavement Testing Facility (PTF) uses rapid pavement testing of full-scale structures to evaluate the durability of both new and existing pavement materials.
